The Importance of Vacuum Pump Check Valves in Industrial Applications
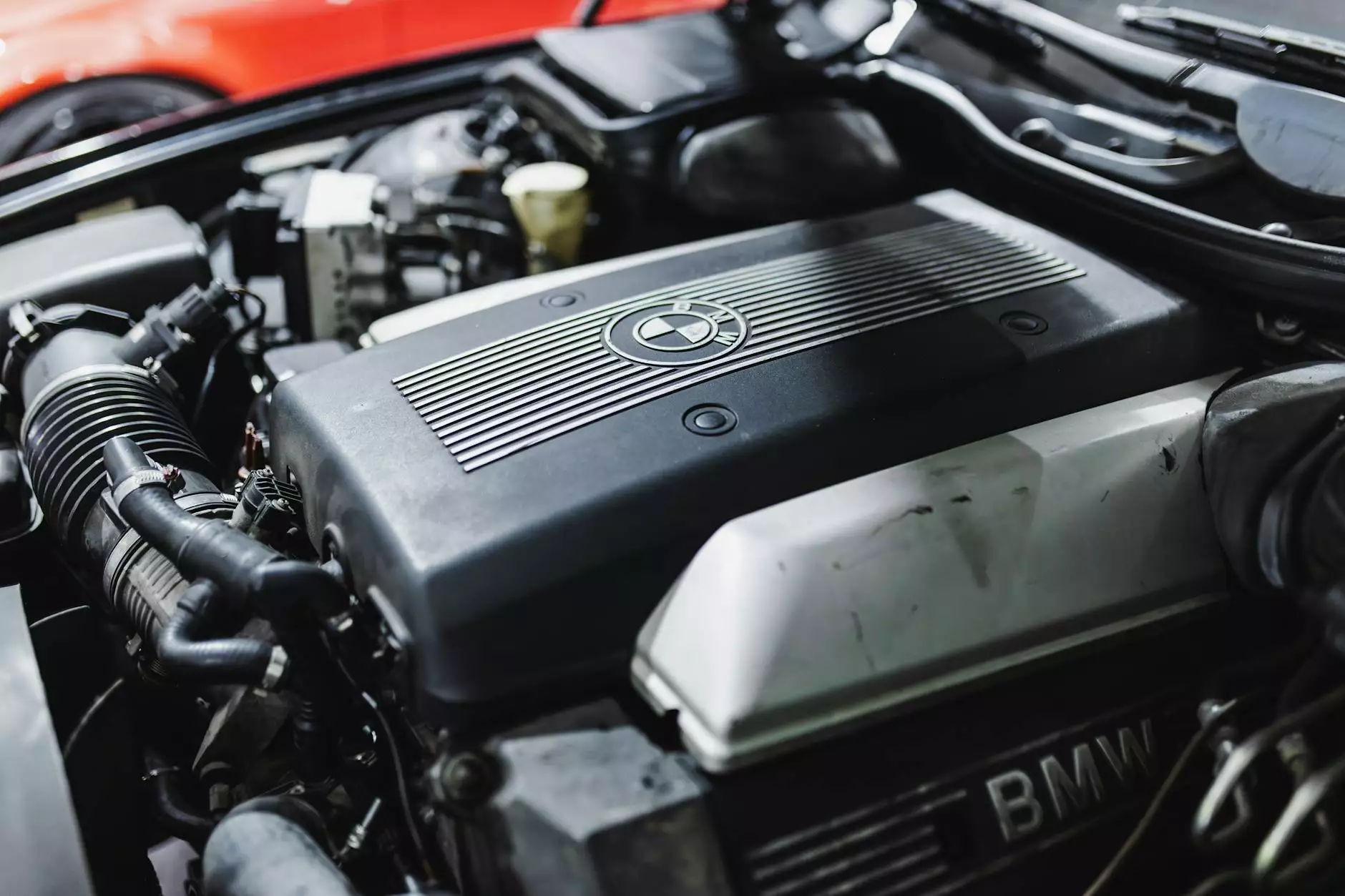
In the realm of modern manufacturing and industrial processes, vacuum pump check valves play a crucial role. They are essential components that significantly influence the efficiency and reliability of vacuum systems. This article dives deep into the functionality, types, benefits, and proper maintenance of vacuum pump check valves, exploring why they are indispensable for industries that utilize vacuum technology.
Understanding Vacuum Pump Check Valves
A vacuum pump check valve is designed to permit the flow of air and gases in one direction, preventing backflow and ensuring that the vacuum system maintains optimal performance. These valves are pivotal in applications where maintaining consistent vacuum levels is critical, such as in packaging, food preservation, electronics manufacturing, and pharmaceuticals.
How Do Check Valves Work?
The operation of a check valve relies on the pressure differential between the inlet and outlet. When the pressure on the inlet side exceeds that on the outlet side, the valve opens, allowing air or gas to flow through. Conversely, if the outlet pressure is higher, the valve closes, thus preventing backflow. This simple yet effective mechanism is crucial for protecting sensitive equipment and ensuring that processes run smoothly.
The Vital Role of Check Valves in Vacuum Systems
Check valves are integral to the functionality of vacuum systems for several reasons:
- Prevents Backflow: By halting reverse flow, check valves protect pumps and other components from potential damage.
- Maintains Vacuum Integrity: Ensures that the desired vacuum level is sustained consistently, which is essential for many industrial processes.
- Enhances System Efficiency: By minimizing energy loss and maintaining optimal pressure levels, check valves contribute to overall system efficiency.
- Cost-Effective Maintenance: The incorporation of check valves reduces the risk of damaging equipment, leading to lower maintenance costs in the long run.
Types of Vacuum Pump Check Valves
Various types of check valves are available, each designed for specific applications and requirements:
1. Spring-Loaded Check Valves
These valves utilize a spring mechanism to close the valve when back pressure is detected. They are simple and reliable, making them suitable for many low to medium vacuum applications.
2. Diaphragm Check Valves
Ideal for applications requiring high cleanliness, diaphragm check valves utilize a flexible diaphragm to prevent backflow. They are commonly used in pharmaceutical applications to avoid contamination.
3. Ball Check Valves
Utilizing a spherical ball, these valves provide a reliable backflow prevention mechanism. They are well-suited for larger diameter pipelines and robust applications.
4. Flapper Check Valves
These are designed with a hinged flap that opens with forward flow. Flapper check valves are effective in applications where space is limited and offer low resistance to flow.
Benefits of Utilizing High-Quality Vacuum Pump Check Valves
Investing in high-quality vacuum pump check valves brings numerous advantages:
- Increased Longevity: Quality materials and design facilitate better wear resistance, extending the lifespan of the valve and the system.
- Precision and Reliability: Well-manufactured check valves provide reliable sealing and precise control, vital in maintaining vacuum levels.
- Improved Safety: By preventing backflow, these valves mitigate the risk of system failures, contributing to a safer work environment.
- Energy Efficiency: Effective check valves help maintain vacuum integrity, reducing the need for pumps to work harder, which saves energy and costs.
Choosing the Right Check Valve for Your Vacuum System
Selecting the appropriate vacuum pump check valve requires consideration of several factors:
1. Application Requirements
Understand the nature of your application. High cleanliness applications may necessitate diaphragm check valves, while robust industrial environments might favor ball check valves.
2. Compatibility with Process Media
Ensure that the materials of the check valve are compatible with the gases or vapors you will be working with. Chemical resistance is vital for maintaining the integrity of the system.
3. Pressure Ratings
Different valves have varying pressure ratings. It is crucial to select a valve that can withstand the pressures of your vacuum system to avoid premature failure.
Maintenance Tips for Vacuum Pump Check Valves
To ensure the longevity and effectiveness of your vacuum pump check valves, regular maintenance is essential:
- Visual Inspections: Regularly check for signs of wear, damage, or misalignment.
- Cleaning: Depending on the application, ensure that the valves are cleaned periodically to remove any build-up that could hinder functionality.
- Regular Testing: Test the check valve operation periodically to ensure that it is functioning correctly.
- Replacement: Plan for replacement of valves as part of regular maintenance to prevent unexpected failures.
Conclusion
In conclusion, vacuum pump check valves are an indispensable component of any vacuum system, impacting not only its efficiency and reliability but also its safety and operational costs. By understanding the types, functions, and best practices for maintenance, businesses can enhance their vacuum systems and ultimately lead to increased productivity. Whether you are looking to buy membranes, silicone membranes, or rubber membranes, it’s clear that selecting the right components for your vacuum systems, including check valves, is paramount. Ensure you choose quality products from reputable sources like vacuum-presses.com to optimize your operations and maintain a competitive edge in your industry.