Unveiling the World of Plastic Injection Molding: A Comprehensive Guide
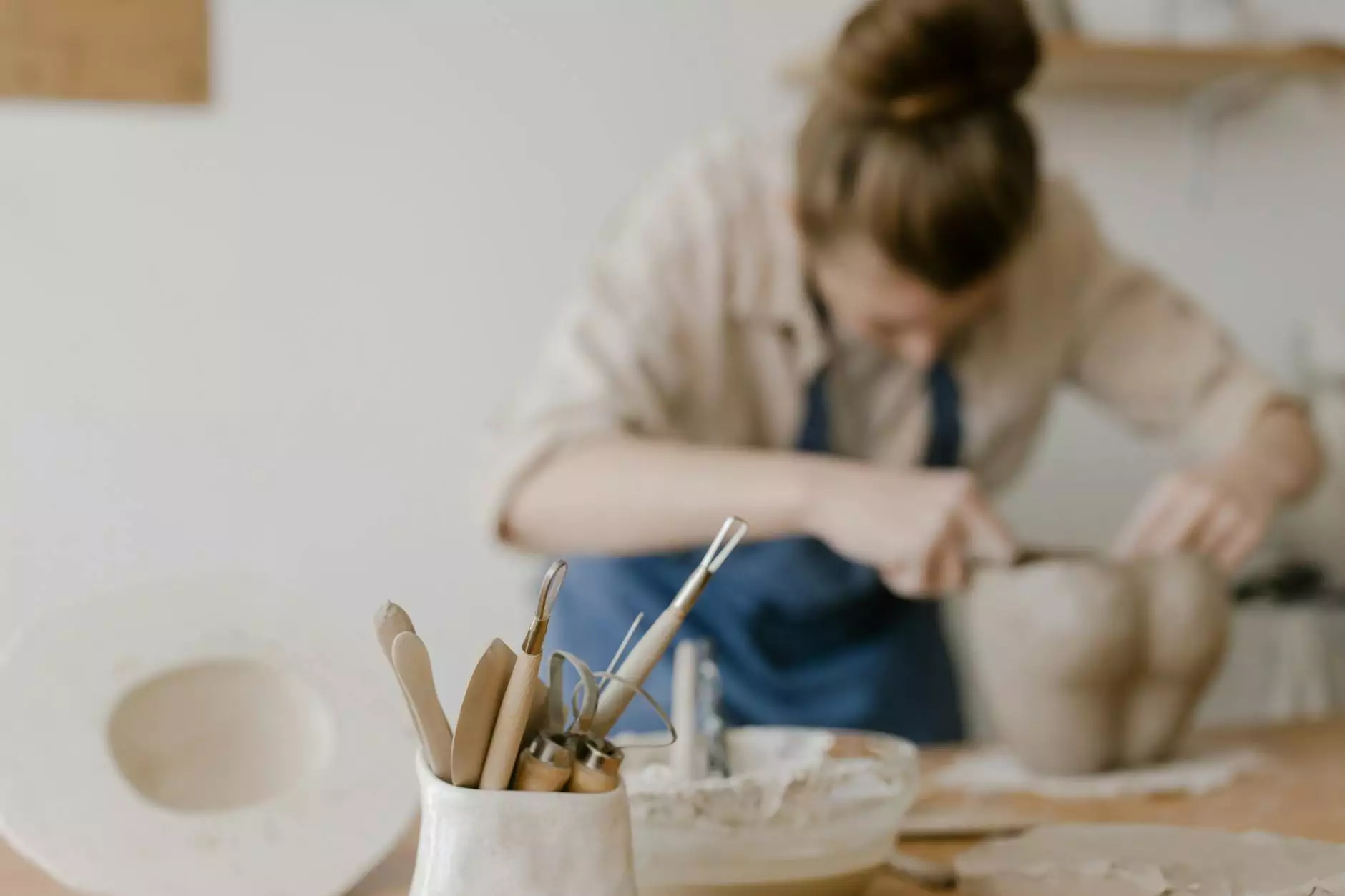
Understanding Plastic Injection Molding
Plastic injection molding is a manufacturing process that involves the creation of parts by injecting molten plastic into a mold. This technique is widely used across various industries due to its efficiency, precision, and versatility. From electronics to automotive components, the applications of this method are extensive and continually growing.
The Process of Plastic Injection Molding
The process of plastic injection molding can be broken down into several key stages:
- Material Selection: Choosing the right type of plastic resin is crucial as it determines the properties of the finished product, including strength, flexibility, and resistance to heat.
- Injection: The selected plastic is heated until it becomes molten and is then injected into a pre-designed mold under high pressure.
- Cooling: Once injected, the plastic is allowed to cool and solidify in the mold, taking its shape.
- Demolding: After cooling, the mold is opened, and the finished part is ejected and prepared for further processing.
- Finishing: The final stage may include trimming, painting, or other finishing processes to enhance the appearance and functionality of the part.
Advantages of Plastic Injection Molding
There are numerous advantages to employing plastic injection molding in manufacturing:
- High Efficiency: Once the mold is created, producing additional parts is quick, making it ideal for mass production.
- Precision: This method allows for intricate designs and high dimensional accuracy, ensuring that parts fit together perfectly.
- Material Variety: A wide range of thermoplastics and thermosetting polymers can be used, enabling customization for various applications.
- Cost-Effective: For large volume production, plastic injection molding reduces the cost per unit significantly.
- Minimal Waste: The process generates very little waste material, contributing to a more sustainable manufacturing effort.
Applications of Plastic Injection Molding
Plastic injection molding is employed in a myriad of sectors:
1. Automotive Industry
In the automotive industry, plastic injection molding is used for producing a range of parts, including:
- Dashboards
- Bumpers
- Interior panels
- Light housings
2. Consumer Electronics
Devices such as smartphones and computers rely on plastic injection molding for components like:
- Casing
- Buttons
- Connectors
3. Medical Devices
The medical field benefits from the precision of plastic injection molding for:
- Parts for surgical instruments
- Hormone injectors
- Medical housings
4. Packaging
Packaging solutions such as containers and caps are frequently produced using plastic injection molding due to its efficiency and ability to create custom shapes.
Choosing the Right Partner for Plastic Injection Molding
Selecting a knowledgeable partner, like Deep Mould, is crucial for successful plastic injection molding. Look for the following qualities:
- Experience and Expertise: Ensure the company has a track record of successful projects in your industry.
- Advanced Technology: A partner should utilize the latest technology and machinery for high-quality production.
- Quality Assurance: Look for firms that have robust quality control processes to ensure consistency.
- Customer Support: Communication is key; your partner should be willing to engage and address your concerns at every stage of the process.
The Future of Plastic Injection Molding
The future of plastic injection molding looks promising as technology progresses. Innovations such as:
- 3D Printing Integration: Combining traditional molding with 3D printing techniques to enhance design capabilities.
- Biodegradable Plastics: Increased focus on sustainability will lead to the use of eco-friendly materials.
- Smart Manufacturing: The integration of IoT and AI will optimize the process, making it more efficient and responsive.
Conclusion
In conclusion, plastic injection molding is a pivotal manufacturing process that supports numerous industries by providing efficient, precise, and versatile solutions. Companies like Deep Mould exemplify the best in the industry by delivering quality and innovative products that meet the needs of their clients. As we move forward, ongoing advancements in technology promise to further enhance the capabilities and sustainability of this vital manufacturing method.