Understanding Electric Plastic Molding: A Game Changer in Manufacturing
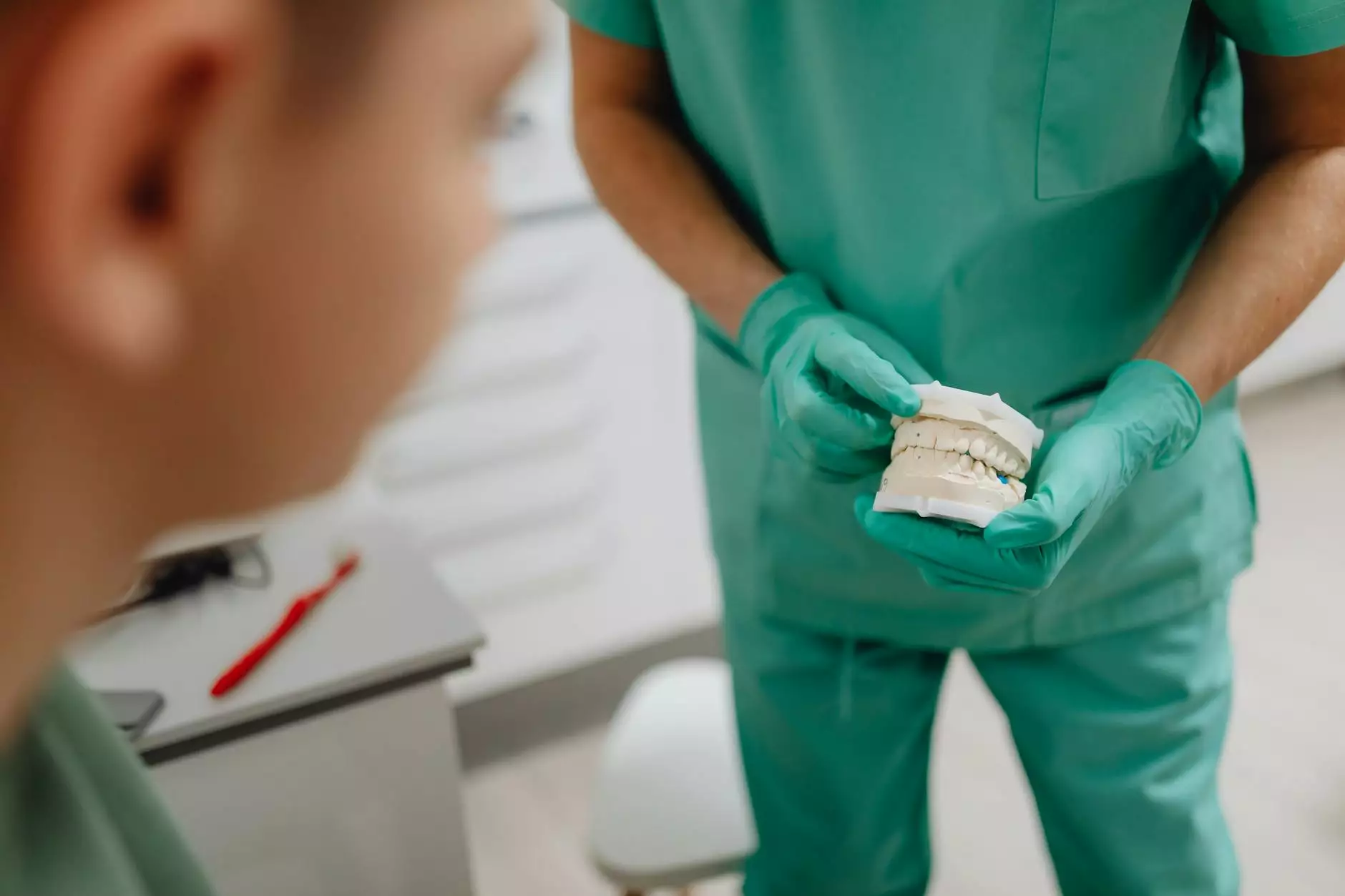
Electric Plastic Molding has transformed the manufacturing landscape, offering innovative solutions across various industries. This advanced technique utilizes electric machinery in the plastic molding process, leading to efficiency, precision, and sustainability. In this article, we will delve into the intricacies of electric plastic molding, its benefits, applications, and how it stands out in the field of metal fabrication.
What is Electric Plastic Molding?
Electric plastic molding is a specific type of injection molding that utilizes electric screw drives and servomotors instead of hydraulic systems. This modern approach provides several benefits compared to traditional molding methods, such as reduced energy consumption, enhanced precision, and minimized environmental impact.
How Does Electric Plastic Molding Work?
The process of electric plastic molding involves several critical steps:
- Material Preparation: The plastic granules are prepared and fed into the hopper of the machine.
- Injection Phase: The electric motors control the screw that melts the plastic pellets and injects the molten plastic into the mold.
- Cooling Phase: Once injected, the plastic cools down and solidifies within the mold.
- Ejection Phase: Finally, the mold opens, and the finished product is ejected smoothly by the system.
The Advantages of Electric Plastic Molding
Electric plastic molding offers several advantages that make it an attractive option for manufacturers, especially in metal fabrication:
1. Energy Efficiency
Electric machines are significantly more energy-efficient than their hydraulic counterparts, which contributes to lower operational costs. This efficiency is particularly beneficial for businesses looking to reduce their carbon footprint.
2. Precision and Repeatability
Due to the precise control of electric motors, electric plastic molding ensures high levels of accuracy and repeatable results. This precision is crucial in industries where tolerances are tight, ensuring that every piece manufactured meets exact specifications.
3. Enhanced Cycle Times
The speed at which electric machines operate allows for shorter cycle times, increasing production rates. Businesses like DeepMould can significantly boost output without compromising quality.
4. Greater Design Flexibility
Electric plastic molding supports complex designs, enabling manufacturers to create intricate parts that might be challenging or impossible to achieve with traditional methods.
5. Reduced Environmental Impact
With lower energy consumption and less material waste, electric molding is a more environmentally friendly option, aligning with sustainable manufacturing practices.
Applications of Electric Plastic Molding
The versatility of electric plastic molding makes it suitable for various sectors, including:
- Automotive Industry: Used to manufacture lightweight components that improve vehicle efficiency.
- Consumer Electronics: Provides precision components for devices such as smartphones and tablets.
- Medical Devices: Ideal for producing high-quality, sterile plastic parts essential for healthcare.
- Packaging Materials: Effective in creating sustainable packaging solutions through efficient molding processes.
Electric Plastic Molding vs. Traditional Methods
To appreciate the advantages of electric plastic molding, it's essential to compare it with traditional hydraulic molding. Here are some key differentiators:
1. Operation Mechanism
Traditional molding relies on hydraulic systems that can consume more energy and require more maintenance. In contrast, electric modules utilize precision servo motors, allowing for finer control during the injection process.
2. Maintenance Costs
Due to fewer moving parts, electric molding machines often incur lower maintenance costs and downtime, making them a more reliable option over time.
3. Quality of Output
Electric molding typically results in higher-quality outputs due to its accurate process controls, whereas traditional methods may lead to inconsistencies.
DeepMould: Pioneering Electric Plastic Molding in Metal Fabrication
At DeepMould, we embrace cutting-edge technologies such as electric plastic molding to enhance our manufacturing processes. Serving the Metal Fabricators category, our commitment to innovation allows us to deliver superior products that meet the evolving needs of our clients.
Why Choose DeepMould?
- Expertise: A team of experienced professionals well-versed in electric plastic molding techniques.
- Quality Assurance: Rigorous quality control measures ensuring product compliance with international standards.
- Customer-centric Approach: Tailored solutions that align with your specific requirements and industry demands.
- Innovative Solutions: Continuous investment in R&D to stay ahead in technology and manufacturing processes.
The Future of Electric Plastic Molding
The future of electric plastic molding looks promising, with ongoing advancements in technology paving the way for even greater efficiency and precision. As industries seek to adopt more sustainable manufacturing practices, electric molding offers a compelling solution by minimizing energy consumption and waste.
Industry Trends to Watch
- Integration of Smart Technologies: The rise of smart manufacturing will lead to the integration of IoT devices to monitor and optimize the molding process.
- Sustainability Initiatives: More companies will adopt electric plastic molding to fulfill their environmental commitments.
- Customization and Personalization: As consumer preferences shift, the demand for personalized products will push manufacturers to utilize electric molding for customizable designs.
Conclusion: Embracing the Electric Plastic Molding Revolution
The shift towards Electric Plastic Molding marks a significant evolution in manufacturing, particularly for businesses engaged in metal fabrication. Its benefits, including energy efficiency, precision, and sustainability, position it as a favorable choice for the future. At DeepMould, we are excited to lead the charge in this transformative field, offering advanced solutions to meet your manufacturing needs. Embrace the electric molding revolution today and discover how it can propel your business to new heights.